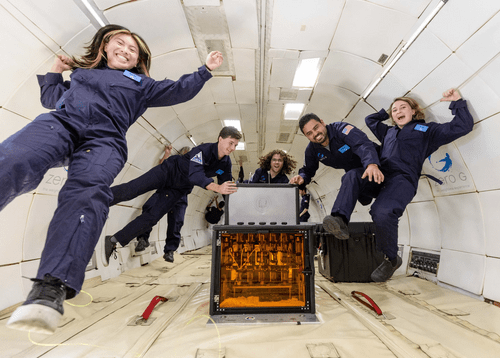
SpaceCAL - 3D Printing in Space
CAL, or Computed Axial Lithography, is a volumetric additive manufacturing technique developed through a partnership with UC Berkeley and Lawrence Livermore National Lab that forms parts out of photopolymer resin, solidified using ultraviolet light. By projecting an image at a rotating vial with photocurable resin, a part is able to be formed, as shown below: [1]
Since this type of 3D printing forms the entire part simultaneously, challenges associated with traditional layer-by-layer systems are avoided (support material, layer marks, flat liquid-gas interface). The application of CAL towards in-space manufacturing could bring the capability to manufacture new types of parts to orbital missions, such as lenses, flexible seals, organic tissue, and microstructures.
The first goal of the project was to improve the existing payload in preparation for Zero-G parabolic flight tests. To support these updates, I modified the framing for ease of access to internal components, increased rigidity of mounts and mechanical structures, and helped to improve optical components (integration of new lenses for improved print quality, development of a particle image velocimetry (PIV) system to accurately capture fluid flow, and other general upgrades to improve the printing process).
In addition to printing, a typical resin-based print cycle consists of post-processing to remove excess resin from the part, as well as curing the print using UV light to provide the part with its final material properties. Since the original printer was only capable of the printing stage, our goal was to introduce a viable post-processing method to the payload. In order to do so, I worked on two different methods of post-processing, centrifugal separation and solvent displacement, to explore which option would be more viable for ISM.
The solvent displacement post-processing method involves displacing the resin the 3D printed part is printed in with isopropyl alcohol while still in the vial. This was accomplished by developing a system of two syringes - one containing alcohol and an empty syringe to collect the displaced resin. When accentuated, the alcohol is pushed through the vial, displacing the resin into the empty syringe, and cleaning the 3D-printed part. Although results from this method were promising, we faced issues keeping the isopropyl alcohol and resin contained. The injection was also activated manually, which meant the displacement was not uniform across samples.
The second post-processing method utilizes centrifugal force to remove excess resin from the surface of the part. Using a motor to spin the vial containing the printed part, the resin is separated from the part and driven towards the outer walls of the rotating vial, where it can then be collected and removed. A cylindrical mesh is used within the vial to retain the part in place and ensure protection from the centrifugal forces. During parabolic test, we also faced issues with resin leakage and keeping the excess resin separated from the print. Applying what I learned from the results of these tests, I designed a simplified test fixture to test the critical components of the centrifugal-based system at various angles to better analyze its viability.
Using this fixture, we were able to confirm that the part would not become damaged during high rates of rotation and that the majority of excess resin could successfully be removed from the part using centrifugal-force. With a combination of further testing and computational fluid dynamics, we could explore various angles to determine the optimal balance between post-processing duration and resin removal efficiency.
Moving forward, the team aims to integrate printing and post-processing into a fully autonomous payload that will operate in a sub-orbital microgravity environment, launched by a sub-orbital flight provider. The next mission will test this comprehensive system in longer microgravity environments and conduct vibrational, thermal, shock, and other tests to ensure the In-Space Manufacturing (ISM) system can withstand the rigors of spaceflight. Our M.Eng team generated the initial requirements and layout for this printing system using specifications provided by the launch provider (Blue Origin), and the proposed design that would achieve this integration is currently being developed by another M.Eng team.
As a result of this project, I have been able to greatly improve upon my knowledge of optical systems, tightly integrated electronics enclosures, and rapid prototyping to develop creative solutions. Our team's efforts to develop space-viable post-processing technologies for the SpaceCAL system have shown promise, and future improvements will continue to refine the system's design and capabilities. These advancements will pave the way for more efficient and effective In-Space Manufacturing, reducing the need for ground-manufactured replacement parts, as well as reducing launch mass and cost.
Figure Credits:
[1] B. Kelly, I. Bhattacharya, H. Heidari, M. Shusteff, C. Spadaccini, and H. Taylor, "Volumetric Additive Manufacturing via Tomographic Reconstruction", Science 2019. doi:10.1126/science.aau7114
[2] "Particle Image Velocimetry (PIV) Principle", Optolution, accessed 6 November 2023.
[3] “New Shepard Payload User’s Guide”, Blue Origin, personal communication, 22 September 2022.